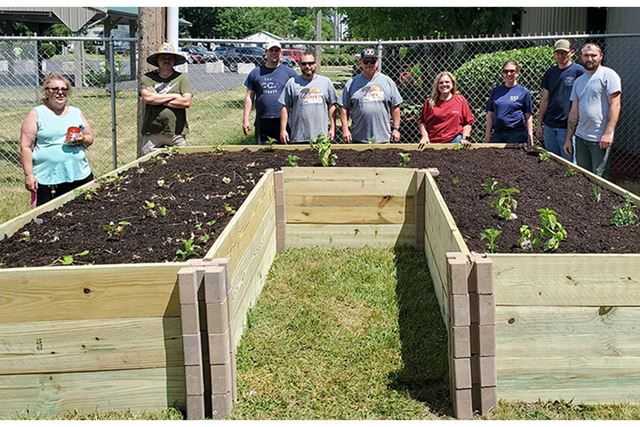
Huhtamaki’s Marion, Ind. location is on a hot streak, and they want to keep it going.
Since the acquisition by Huhtamaki in 2012, the facility has undergone significant changes and grown from a respected regional company to a top supplier for the country’s largest retailers. The facility manufactures paperboard pressed plates sold by numerous grocery stores and large national retailers.
The team and their products recently took home an award as Private Label Vendor of the Year from Dollar General, and they work to make their operations sustainable as they approach four years of zero waste to landfill and reduce water usage.
Award-winning products in Marion
Marion and Huhtamaki’s product management/sales teams leveraged a long-standing relationship with Dollar General to significantly grow their business by producing unique and fun designs for their seasonal paper plate offerings.
The Marion team was able to deliver with a flexible production environment that meets the needs of large national customers and gives them a unique service offering.
Sending zero waste to landfill and reducing water usage
The team took its first steps toward getting rid of waste, in 2021, by making sure they identified all materials that could be recycled. Everything, including metal, paper, water and even paper dust, was analyzed to see if it could be recycled.
Materials that could not be recycled go to a local waste-to-energy facility that converts the waste into electricity for the area.
The end result is a facility that sends no waste to landfills.
”On top of everything we learned from our sustainability efforts, we also learned that our team really enjoys a challenge,” Jamie Huller, Marion Plant Manager said. ”They really come together behind this goal and take pride in maintaining our zero waste culture much the same way they are proud of the products we make.”
Next stop, water consumption
With waste handling ingrained in the facility’s ways of working, the team turned its attention to reducing the amount of water used and found an opportunity in the humidification system.
Companies that convert paper into food packaging products often pump moisture into the air to aid in the forming process. What the team quickly realized was that the need for humidification fluctuated depending on conditions inside and outside the facility.
The team then installed an automated system that switched on when humidity dropped below a set level and made sure that moisture was delivered only in needed areas.
This simple fix reduced overall water usage by 55 percent.
Leading in their community
Throughout their history, Marion employees have volunteered in the community supporting beautification projects, food drives, education, delivering material donations, or organizing charitable events; this team is ready to help where needed.
They aren’t just participating in community outreach; they are leading the charge.
Human Resources Manager Kristi Pulley serves on the Grant County Economic Development Council, while Huller works on the local YMCA Board of Directors and will soon be Chair. This is in addition to their dedicated service to the nearby St. Martin Community Center.
“It’s very important that we not only support our community, but take the lead,” Pulley said. “We want to be a positive force in our community and our employees feel an extra sense of purpose and belonging when they can contribute to improving the place where we live.”
The Marion facility is hiring
Marion recently made significant improvements to the working environment with an improved air conditioning system in the production areas. They offer skill development, opportunities for rapid advancement, and they want you to apply.
Go to us.huhtamaki.com/careers, navigate to the Marion, Ind. location on the left side page and apply today.